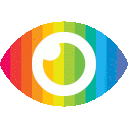
1. Researchers have developed a wearable capacitive sensor that can respond to both normal pressure and shear force, using a spine-shaped dielectric layer formed through magnetic field-assisted in situ assembly.
2. The sensor exhibits sensitive pressure monitoring with a detection limit of 2 Pa and reliable and recoverable shear perception with a sensitivity of 0.0752 N−1 (0.015–0.50 N) and 0.0177 N−1 (0.50–1.30 N).
3. The device has potential applications as a wearable motion indicator, artificial intelligence, and body force sensor in terms of pressure and shear force recognition, thanks to its facile production, competitive detection performance, and capability of pressure-shear monitoring.
The article titled "In situ assembly of a wearable capacitive sensor with a spine-shaped dielectric for shear-pressure monitoring" published in the Journal of Materials Chemistry C presents a new approach to creating flexible sensors that can monitor both pressure and shear force. The article highlights the potential applications of such sensors in wearable electronics, healthcare monitoring, and artificial intelligence.
The article provides a detailed description of the methodology used to create the spine-shaped dielectric layer for the capacitive sensor. The authors claim that their approach is template-free, facile, and can induce a highly compressible medium for pressure sensing while simultaneously enabling sustainable shear force monitoring. The capacitive sensor is said to exhibit sensitive pressure monitoring with a detection limit of 2 Pa and reliable and recoverable shear perception with a sensitivity of 0.0752 N−1 (0.015–0.50 N) and 0.0177 N−1 (0.50–1.30 N).
While the article provides detailed information about the methodology used to create the sensor and its performance characteristics, it does not provide any information about potential risks associated with using such sensors in wearable electronics or healthcare applications. Additionally, there is no discussion of any limitations or drawbacks of the proposed approach.
The article also appears to be somewhat promotional in nature, highlighting the potential applications of the sensor without providing much detail on how it compares to existing technologies or addressing any potential challenges associated with its implementation.
Overall, while the article provides interesting insights into a new approach to creating flexible sensors for pressure and shear force monitoring, it would benefit from more balanced reporting that addresses potential risks and limitations as well as alternative approaches to achieving similar results.