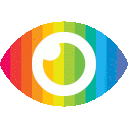
1. Duplex stainless steel (DSS) obtained by directed energy deposition additive manufacturing (DED) has a non-uniform ferrite to austenite microstructure, limiting its properties.
2. A fast numerical modelling approach was developed to predict and optimize the phase ratio distribution in DSS formed by DED, with a proposed temperature control strategy of the build platform to achieve near 50-50 phase ratios.
3. The proposed approach was validated through experiments on single-bead-thickness walls of SAF 2507 superduplex stainless steel, with reasonable agreement between numerical and experimental results observed.
The article presents a study on the directed energy deposition (DED) additive manufacturing process of duplex stainless steel (DSS). The authors aim to develop a fast numerical simulation of temperature and diffusion-controlled ferrite to austenite phase transition of DSS obtained by DED in order to determine process parameters and temperature control systems enabling them to reach a targeted microstructure, namely a rather uniform and balanced ferrite/austenite ratio. The proposed model is validated on experiments, which assess the microstructures and proportion of austenite to ferrite in single bead thickness walls of SAF 2507 super-duplex stainless steel obtained via LMPDED.
The article provides a comprehensive overview of the challenges associated with AM processes for DSS, including the unpredictability of product properties such as porosity, microstructure, and residual stresses. The authors highlight that optimal properties generally require near 50-50 ferrite-austenite duplex microstructures, which are difficult to achieve through AM processes due to non-uniform solid-state phase transitions. The article also discusses various numerical approaches used in previous studies to compute temperature fields in LMPDED.
The authors propose a fast numerical approach that can deal with more complex geometry and takes into account latent heat release during solidification. They also derive a fast diffusion-controlled growth model based on semi-analytical developments. The composition at the austenite/ferrite interface is assumed to be at equilibrium, therefore an equilibrium computation has been carried out with Thermo-Calc, which is used as inputs for the diffusion model.
The experimental study conducted on SAF 2507 DSS walls built via DED using a BeAM Mobile-004 machine equipped with an Itterbium YLR fibre laser (1070 nm wavelength) and a 500 W maximum power output validates the proposed approach. Microstructures and phase ratio gradients are assessed in single-bead-thickness walls of SAF 2507 superduplex stainless steel, and numerical results are in reasonable agreement with experimental observations.
Overall, the article provides valuable insights into the challenges associated with AM processes for DSS and proposes a fast numerical approach that can help optimize process parameters to achieve targeted distribution of phase ratios. However, it should be noted that the study only focuses on one specific type of DSS (SAF 2507), which limits its generalizability. Additionally, while the proposed approach is validated through experiments, further studies are needed to assess its applicability across different types of DSS materials and AM processes.