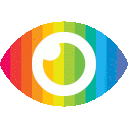
1. The study aimed to predict the depth of impressions obtained by pneumo-ball peening using a dynamic ball-peening process model.
2. The formula obtained from the model allows for the calculation of the depth of post-machining impressions, which was experimentally verified with satisfactory results.
3. By controlling parameters such as ball diameter, mass, and impact speed, it is possible to predict and influence the results of ball peening treatment, including the maximum height of surface unevenness.
The article titled "Predicting the height of uneven surface after ball-peening machining" provides an overview of the process of ball peening and its impact on the machined surface. The article highlights that existing theoretical formulas do not include machining parameters, and therefore, a dynamic ball peening model is required to predict the maximum depth of impressions.
The article presents a detailed analysis of the theoretical basis for predicting the depth of post-machining impressions. It describes how a system of equations can be used to calculate the depth of impressions based on process parameters and material properties. The article also discusses experimental verification of this formula with satisfactory results.
However, there are some potential biases in this article that need to be considered. Firstly, the article focuses primarily on the benefits of ball peening and does not provide a balanced view of its potential risks or limitations. For example, it does not discuss any negative effects that may arise from using high-pressure equipment or steel balls with low hardness.
Secondly, while the article acknowledges that some previous studies have derived mathematical relationships between surface coating parameters and surface roughness, it does not explore these findings in detail or consider their potential relevance to predicting impression depths.
Thirdly, the article assumes that universal parameters such as diameter and mass of balls and speed of impact can be controlled on each ball peening stand regardless of its constructional features. However, this assumption may not hold true in practice as different machines may have varying capabilities or limitations.
Overall, while this article provides valuable insights into predicting impression depths after ball-peening machining, readers should be aware of its potential biases and limitations. Further research is needed to fully understand the benefits and risks associated with this process.