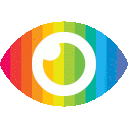
1. A modified 3D printer and open slicing step were used to produce continuous carbon fiber reinforced PolyAmide (cCF/PA6-I) with reduced porosity and improved mechanical properties compared to a commercial printer.
2. The thermomechanical performance of the 3D printed cCF/PA6-I composites was characterized along different printing directions (-55 to +100°C), with transverse and in-plane shear stiffness and strength being particularly sensitive to temperature variations due to the high sensitivity of the polymer matrix, fiber/matrix, and interfilament interfaces.
3. Fractography revealed damage mechanisms induced by internal thermal stresses, highlighting the importance of understanding the behavior of 3D printed composites in severe environments or for developing thermally active 4D printed composites.
The article "Thermomechanical performance of continuous carbon fibre composite materials produced by a modified 3D printer" presents a study on the mechanical properties and microstructure of continuous carbon fiber reinforced polymer composites (CFRPC) produced by a custom-made 3D printer. The authors compare their results with those obtained from a commercially available Markforged® MarkTwo printer. They also investigate the effect of temperature on the mechanical behavior of the printed CFRPC samples.
The article provides valuable insights into the potential of 3D printing for producing complex composite structures with tailored cost and environmental impact. The authors highlight the importance of controlling print quality to develop robust and reliable manufacturing processes and print structures. They show that their custom-made printer, together with an open-source slicing software, allows better control over print conditions, resulting in reduced porosity and improved mechanical properties compared to samples printed with a commercial printer.
However, the article has some limitations that need to be addressed. Firstly, it lacks information on the reproducibility of the results obtained from their custom-made printer. It would be interesting to know if other researchers can achieve similar results using their printing parameters or if there is a high degree of variability between different printers.
Secondly, while the authors discuss the effect of temperature on the mechanical behavior of CFRPC samples, they do not provide any information on how these materials perform under other environmental conditions such as humidity or UV exposure. This limits our understanding of how these materials behave in real-world applications where they may be exposed to multiple stressors simultaneously.
Thirdly, while the authors acknowledge that interfilament distance is an important parameter for controlling porosity in printed CFRPCs, they do not provide any information on how this parameter affects other mechanical properties such as fatigue resistance or fracture toughness. This limits our understanding of how different printing parameters affect overall material performance.
Finally, while the article provides valuable insights into the potential benefits of 3D printing for producing complex composite structures, it does not address any potential risks associated with this technology such as emissions from printing materials or disposal issues related to waste generated during printing.
In conclusion, while "Thermomechanical performance of continuous carbon fibre composite materials produced by a modified 3D printer" provides valuable insights into the potential benefits of 3D printing for producing complex composite structures with tailored cost and environmental impact, it has some limitations that need to be addressed. Future research should focus on addressing these limitations to further advance our understanding of how 3D printing can be used to produce high-performance composite materials for real-world applications.