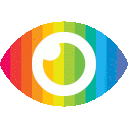
1. Electrohydrodynamic jet (E-Jet) technology uses electrical and hydrodynamic forces to pattern structures with high resolution and material adaptability.
2. Coaxial electrohydrodynamic jet (CE-Jet) technology, which uses a coaxial needle system, has the potential to produce nanoscale structures with a relatively large-sized needle.
3. Numerical simulation using the Navier-Stokes equation and phase-field method can help optimize parameters and working conditions for CE-Jet printing of nanoscale structures, as demonstrated in experiments using photoresist and lead zirconate titanate as inner liquids.
The article titled "Numerical simulation of coaxial electrohydrodynamic jet and printing nanoscale structures" provides an overview of the electrohydrodynamic jet (E-Jet) technology, which is used for patterning structures using electrical forces and hydrodynamic force. The article focuses on the coaxial electrohydrodynamic jet (CE-Jet) system, which is capable of producing multilayered composite structures. The authors discuss the theoretical analysis of the CE-Jet process and its numerical simulation using computational fluid dynamics (CFD) model in COMSOL multiphysics.
The article provides a detailed description of the forces acting on the CE-Jet system, including surface tension, gravitational force, electrical force, viscous force, and dielectric force. The authors also discuss the use of phase-field method to track the interfaces of inner-outer liquid and outer liquid-air. They present a three-phase flow model to study the formation of CE-Jet and investigate the influences of applied voltage and inner solution flow rate on the morphology and size of inner jet.
The article also discusses the experimental work conducted under optimized working conditions obtained from simulation. The stable CE-Jet consisting of inner nanoscale jet of functional material and outer microscale jet of high viscous liquid was formed. After printing and removing the outer high viscous liquid (silicone oil in this work), the authors obtained inner nanowire structures of photoresist (AZ703) with a diameter of 85 nm and lead zirconate titanate (PZT) with a diameter of 70 nm.
Overall, the article provides valuable insights into CE-Jet technology for printing nanoscale structures. However, there are some potential biases in this article that need to be considered. Firstly, there is a lack of discussion on possible risks associated with CE-Jet technology such as toxicity or environmental impact. Secondly, while discussing previous works on CEA process simulation, there is no mention about any limitations or drawbacks associated with those studies.
Moreover, while discussing experimental work conducted under optimized working conditions obtained from simulation, there is no mention about any challenges faced during experimentation or any limitations associated with their results. Additionally, there is no discussion about any counterarguments or alternative approaches to CE-Jet technology.
In conclusion, while this article provides valuable insights into CE-Jet technology for printing nanoscale structures through both theoretical analysis and experimental work, it has some potential biases that need to be considered. Further research should be conducted to address these biases and explore alternative approaches to CE-Jet technology.